Tag: cabinet making training
2020 Cabinetry and Woodworking Trends Everyone in Cabinet Making School Should Know About
August 27, 2020Whenever cabinets or woodwork need a fresh, modern update, there are several routes you can take. You can pick certain colours, or mix and match several of them. You can take a minimalist approach to a room’s design, or you can match traditional kitchen aesthetics with more open-concept designs.
Regardless of which route you take, your job as a cabinet maker is to bring these aesthetic decisions to life. If you want to keep it as fresh as possible, consider choosing from any of the trends we’ve listed below!
Here are some cabinetry and woodworking trends in 2020 you should be aware of.
Mixed Colours and Two-Tone Designs Are In for Today’s Kitchen Cabinets
While monochrome colour schemes for cabinets can tend to dominate certain kitchens, mixing them up is among the biggest trends for 2020. In particular, two-tone cabinets are seen as being on the rise, particularly since they can help make the room seem more expansive and dynamic-looking.
Creating a contrast between two different colours for cabinets can also add greater texture to the room and make the design stand out. A move away from traditionally-coloured kitchen cabinets is one that students in cabinet making school shouldn’t be surprised to see–whether it’s a combination of neutral, saturated or bright tones.
Finding Innovative Ways to Make More Storage Room is Another Hot Trend
If your cabinetry or woodworking project involves a living space that is smaller in size, the use of space becomes increasingly important. Therefore, finding ways to create a greater storage capacity and avoid wasting space is something else that should be at the top of your mind for 2020.
One way to do this is with custom cabinets, which can be used to make better use of tight spaces. Another is by getting creative with the cabinetry you’re working on in order to avoid overloading drawers unnecessarily.
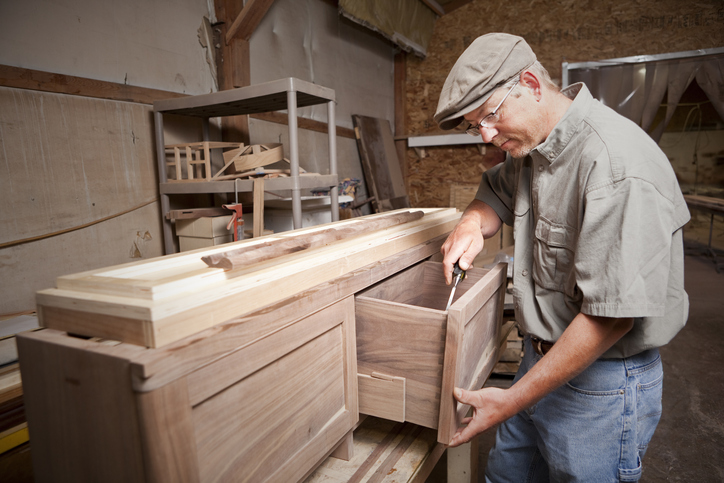
For example, you could designate cabinets and drawers for garbage or recycling, have roll-out drawers and trays for varying purposes, or create dividers for kitchen materials such as utensils. With making better usage of space a hot topic in recent months, you have an opportunity to help homeowners do it in practical and clever ways.
Cabinet Making School Students Should Take Note of Open-Concept Designs
Those doing their cabinet making training will surely appreciate how open-concept designs are becoming more of a trend in 2020 as well. This is especially the case with open-frame cabinets and open shelving in kitchens, getting rid of upper kitchen wall cabinets entirely, or a mix of both.
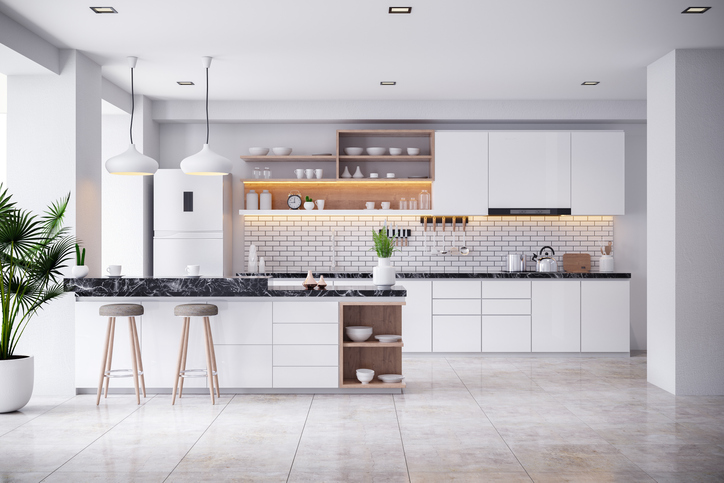
These can look great from a design and aesthetic standpoint (for example, if you’re using rough-cut wood), as well as in helping make the room appear bigger. Better yet, it can put the house owner’s dishes on display for everyone to see, help them be more creative and productive with how they use space on their countertops, and also showcase their penchant for careful placement and organization.
Want to take cabinet making courses?
Contact North American Trade Schools for more information!
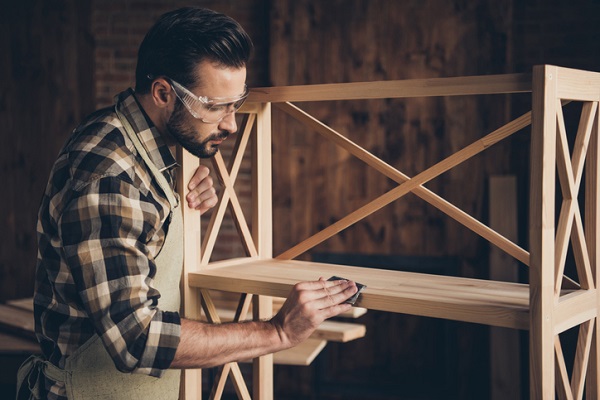
To the untrained eye, all wood types may appear somewhat similar, apart from slight variations in colour. However, cabinet makers know that not all woods are created equal. Each has its own grain, texture, and density that makes it well-suited for a particular purpose – and it’s up to cabinet makers to discover what that purpose is.
Generally speaking, hardwoods like maple and hickory are great for projects requiring sturdy framing, whereas softer woods like fir and spruce are ideal for pieces like baseboards and wall studs. But even within these two overarching categories are a wide variety of wood types with unique characteristics.
If you’re interested in cabinet making school, read on to learn all about the popular types of wood you’ll encounter in your studies!
Pine: A Popular Wood Type for Construction
This lightweight softwood is an excellent choice for structural projects such as roof trusses and joists because it is unlikely to swell and shrink. Couple that with its amber colouring and knotty characteristics and you’ve got a wood type that adds a rustic effect to cottages, cabins, lodges, and more. If your pine project is exposed to the elements, however, it’s important to treat it beforehand to prevent it from rotting over time.
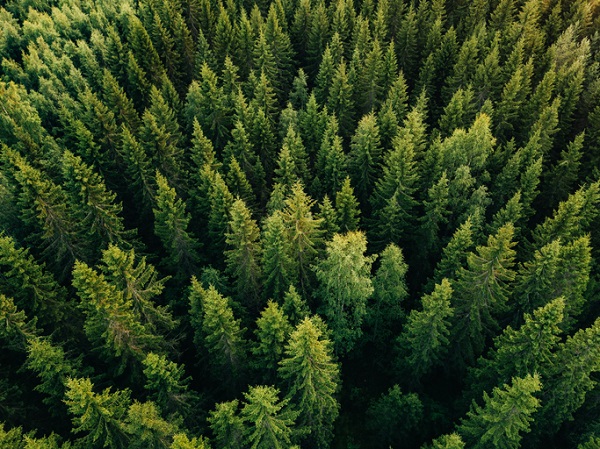
Maple: A Durable Wood Cabinet Making School Graduates Will Love
With a smooth, even wood grain and an ability to work well with a variety of finishes, maple is a popular choice for home decor pieces. It is also one of the hardest types of cabinetry wood, making it great for durability as well as design.
Maple cabinets usually come in a creamy white hue, but a cabinet door panel may feature some reddish-brown colouring. You will also find yellow and pink tones in the wood, along with tan coloured mineral streaks that darken with stain.
Oak: A Common Wood You’ll Encounter in Cabinet Making Courses
If you’re interested in cabinet making training, you’ll quickly learn about the power and popularity of oak. This versatile wood has been used in fine furniture for years and offers numerous variations to suit a wide variety of projects.
Red oak – especially selections with complex flame or arched grain patterns – is one of the most popular hardwoods for cabinets. White oak, in contrast, offers straighter grains but tends to be more expensive.
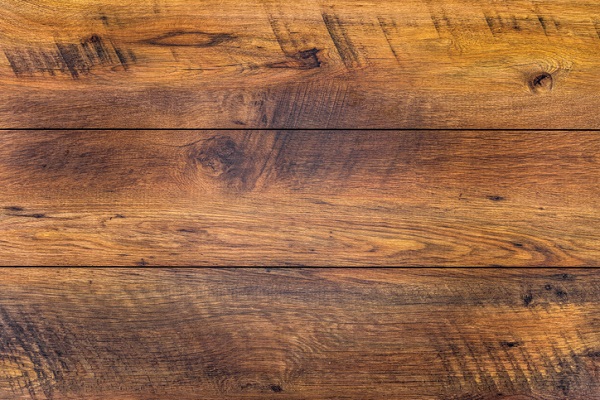
Spruce: A Sturdy Wood Selection for Cabinet Makers
If you’re looking for the perfect wood type for economy or utility purposes, spruce fits the bill. When it comes to softwoods, spruce is more dense and solid than pine. However, its straight grain exhibits less character than other softwoods, so it’s used more for its strength than its style.
Curious to learn more about cabinet making courses?
Contact NATS for more information about our programs.
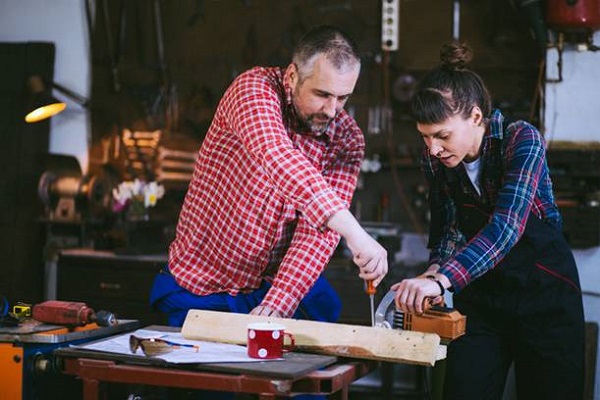
However, many of the tools and techniques that are still used today are rooted in history. For example, many hand tools are variations of those used in Ancient Greek, Roman and Egyptian traditions.
Read on to discover more about the history of cabinet making and its lasting impact on the trade today.
Earliest Examples of Woodwork and Cabinet Making
By definition, cabinets are furniture used to store things and usually feature doors, drawers and/or shelves. It’s thought that early human civilizations used wooden cabinets to protect food products and fire wood from rain and vermin. Archeologists have found evidence that Neanderthals used stone and bone to work wood over 300,000 years ago – which is probably how the first ever cabinets were made!
In the Renaissance era, cabinets became more prestigious items, and would be made of precious wood and feature intricate detailing like marquetry. The cabinet was no longer just a simple storage unit – it was a work of art.
André Charles Boulle was one of the most famous cabinet makers of this era, and his work remains on display at museums and galleries across Europe. It’s well worth seeking these pieces out at some point in your cabinet making training if you want to see the work of a true master of the craft.
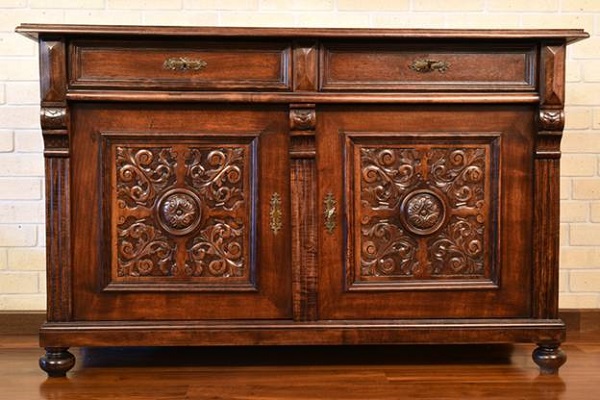
Around this time, cabinets were used to store paper and valuable possessions. Cabinet makers started to introduce writing areas, which led to the invention of bureaus and desks with cabinets.
Cabinets were made larger and larger, and were often the most dominant piece of furniture in a room. All of this combined meant that cabinet makers were one of the most highly regarded woodworkers.
The Industrial Revolution and Introduction of Power Tools Used in Cabinet Making Training
The industrial revolution in the 18th century impacted almost all trades. Electricity was then invented in the mid-19th century, and these two factors changed the cabinet making trade forever.
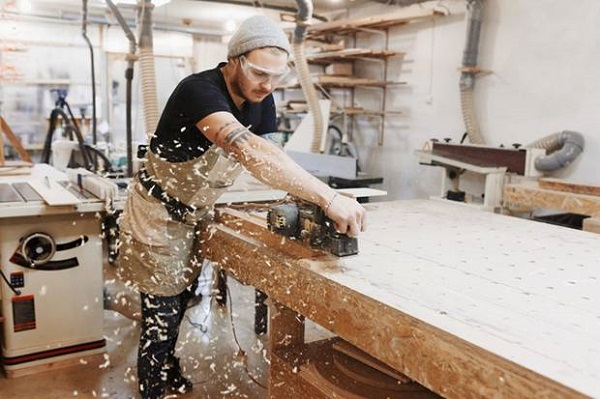
The industrial revolution changed the cabinet making industry forever
The circular saw was invented at the end of the 18th century, and meant that cabinet makers and carpenters could cut wood much faster. And in 1895, the first ever electric hand drill was invented. Variations of both of these inventions are still used in cabinet making courses today.
Cabinet Making Post-World War 2
In the 1950s, cabinet making became a popular hobby. People would spend time designing and building their own bespoke cabinets.
For professional cabinet makers in the 1950s, technical advances were continuing to transform the trade. The invention of numerical control machines meant that cabinet makers could now ensure that they were cutting all wood the same length and dimension without having to spend time measuring and double-checking.
The Cabinet Maker Today
Nowadays, cabinet makers need to know how to cut, shape, and join wood, and they need to be familiar using hand and power tools. Cabinets themselves have also changed. A cabinet is no longer the centre of the room, but often refers to built-in kitchen and bathroom cabinets.
While the cabinet making trade has changed throughout history, it remains an in-demand profession worldwide, and a very rewarding one.
Are you interested in cabinet making courses?
Contact North American Trade Schools to find out more!
A Guide to Architectural Millwork If You’re Considering Cabinet Making School
December 12, 2019Architectural millwork adds to the aesthetics of a building and is often a major part of what people notice and remember about a structure. Produced in a mill, millwork is manufactured to create decorative elements both for the interior and exterior of a building. Millwork can refer to doors, crown molding, baseboards, mantels, window casings and more.
Cabinet making is a skill that can lead to work in this field, as both require a technical and creative understanding of woodwork. Millwork also requires a good understanding of many elements, since building directly into a structure means interacting with other parts of it. Read on for some more things you should know about architectural millwork before graduating!
Millwork After Cabinet Making School Requires Diverse Knowledge
Millwork involves building decorative wooden elements directly into a building. Things like plumbing and lighting are affected by this, as these elements can interact with one another. Having a good basic knowledge of other trades is helpful and it is essential to know where elements are located in a structure to avoid problems or interference.
Since millwork is usually custom made, every job will be unique. The more diverse and extensive your knowledge is, the more you will be able to adapt to different rooms or environments when doing millwork. The projects you encounter will have to adapt to various layouts, dimensions and requirements. Cabinet making school is a great place to start understanding different types of projects and how to keep track of measurements and designs.
Architectural Millwork on Exteriors After Cabinet Making School
Architectural millwork refers to millwork made to fit in with the (often exterior) decor of a building. This could be elements such as trim and more elaborate details on the outside of a structure, like accents and moldings. Usually, exterior architectural millwork is done before millwork on the inside of a building. Architectural millwork can be done in a variety of styles and can be highly individualized.
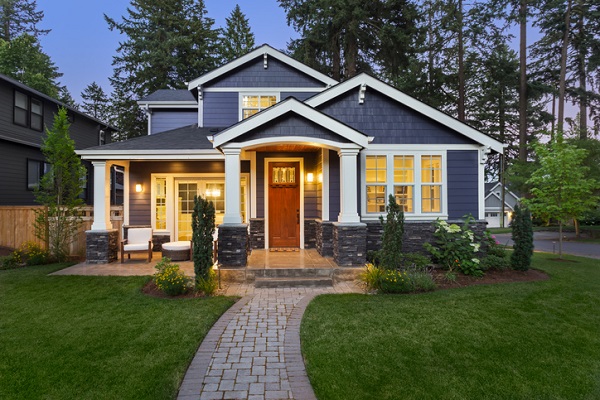
An example of variation in exterior moldings is classical or ancient moldings versus gothic and medieval. The former have Grecian/Roman influence, while medieval and gothic styles draw from flora and fauna for inspiration.
Why Cabinet Making Matters for Architecture
A major difference between millwork and mass-produced pieces is the element of customization. When mass-produced pieces are used in spaces, they cannot be adapted to specific layouts or dimensions. This interferes with the overall look and style, which is important for architectural value. With customized pieces, woodwork can be designed and created to fit with the space, instead of finding a way to make the space work with the piece. Cabinet making training may lead you to working in the field of architectural millwork, which allows more opportunity for beauty and cohesive design.
A very important part of cabinetmaking is choosing materials. In custom projects, materials can make the difference when trying to achieve a look. Not only lumber, but also hardware for cabinets will affect the way that they are received. Architectural millwork can be a fulfilling path if you are interested in combining creativity with technical knowledge to improve spaces and environments.
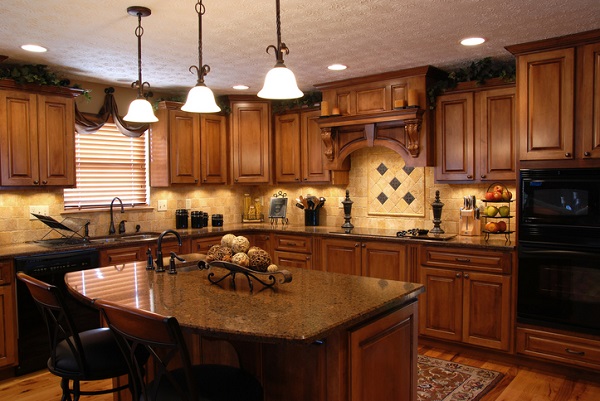
Are you interested in cabinet making courses?
Contact North American Trade Schools to learn more.
How to Juggle Multiple Tasks in Your Career after Cabinetmaking Training
November 12, 2019As you may already know, there are many elements involved in the business of cabinetmaking. You might work in a commercial setting, for a custom furniture maker or within a construction firm. Whatever the work setting is, you must be able to manage the small tasks that help you reach your main goal of making well-crafted woodworks.
If you are self-employed it will become even more important to know how to juggle tasks. You may have to set aside time to communicate with clients about future jobs, update them on current work, and invoice for completed pieces.
In any case, the need to multi-task or manage multiple jobs means that your work is in demand and that is a good thing. On top of having a positive attitude, here are a few suggestions to help you along the way.
Make Checklists
If you have done cabinet making training you will be familiar with reading blueprints, creating designs and making material lists for projects. Checklists play a similar role to these things whether you are doing one job or multiple jobs. They are a helpful way to break down a project and have been proven to reduce errors and increase productivity.
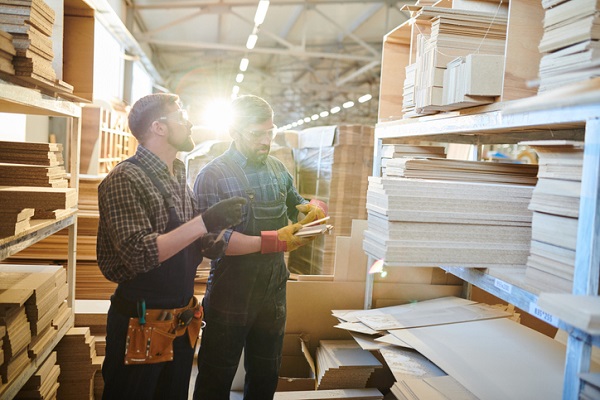
Checklists will also make sure that you provide consistent and reliable service to each client or for each job. This will put you in good standing to be recommended for more work. Also, writing a checklist will help you devise a plan by creating a work sequence or separating a job into several smaller tasks. This will keep you organized and encourage productivity by giving you a sense of accomplishment as you progress through each work day.
Know Your Limits
It is important to have a realistic idea of how much work you can do in a day, week or month. There will be an amount that you can do that will be optimal for productivity and work-life balance. Knowing your limits is also a matter of safety. You do not want to be stressed out or overtired when you are working with machinery and doing precision woodwork.
Understanding how much work you are able to accomplish in a given amount of time will also help you guarantee that your work is of the highest quality. After all, you will want to prioritize applying the skills you worked hard to develop in cabinetmaking school for each project you do.
Use The Skills from Cabinetmaking Training to Focus
If you are thinking of becoming a cabinetmaker it is likely you are creative and detail oriented. In order to maintain a high level of detailed work, it is necessary to be able to focus. Of course, your capacity to focus will be greater if you have already engaged with the other strategies mentioned above.
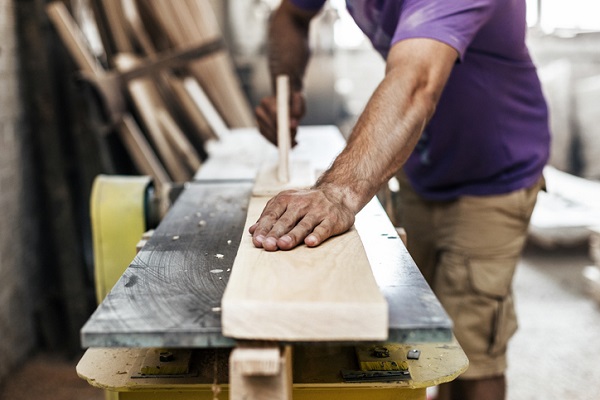
The last thing you want is to be thinking about the materials for one project while you measure and cut pieces for another project. This can lead to mistakes or lower quality work. Juggling multiple tasks means that you are able to focus on the current task because you have set up a realistic plan to get your work done. Paying attention to the work in front of you will also let you enjoy the craft and your own creativity.
Do you think cabinetmaking training is right for you?
Contact North American Trade Schools for more information.
Cabinetmaking is a craft that combines the traditional art of carpentry with the most sophisticated woodworking instruments. For someone who enjoys woodworking, learning about cabinetmaking can open up exciting career opportunities. While cabinetmaking encompasses everything from the identification and selection of the finest wood, to the reading of designs, to the operation of woodworking equipment, one aspect remains perhaps the most critical: safety.
The skills that you learn in cabinetmaking school must be applied with safety always at the top of your mind. If you might be interested in a career as a cabinetmaker and you want to avoid injury, keep reading to learn some essential safety tips!
1. Where You’re Working is as Important as How You’re Working
When working in cabinetmaking, you might decide to eventually begin your own business or simply do some projects on the side in your workshop. Ensuring that the space you work in is safe should be a top priority.
If you, like many woodworking specialists, decide to set up your headquarters in your personal garage or on your property, you need to make sure that the space meets safety standards. You must consider suitable ventilation, fire hazards, and emergency protocol. Remember that while you may not be in a commercial shop, you too must take safety just as seriously if you decide to go out on your own after cabinetmaking school!
2. What You Wear Can Help Protect You from Safety Hazards
Every woodworker should have the right personal protective equipment (PPE) to wear. While sporting the appropriate PPE might seem an obvious recommendation, injuries as a result of non-adequate protection represent a significant percentage of woodworking injuries. One of the reasons for this, ironically, is expertise. Sometimes, when a professional feels overly confident in their abilities, they decide to omit some of the basic PPE. And although they have achieved mastery of their craft, certain things cannot be predicted regardless of experience. A malfunctioning piece of equipment kicking back and chipping a particle of wood or metal into an unprotected eye can cause irreversible damage!
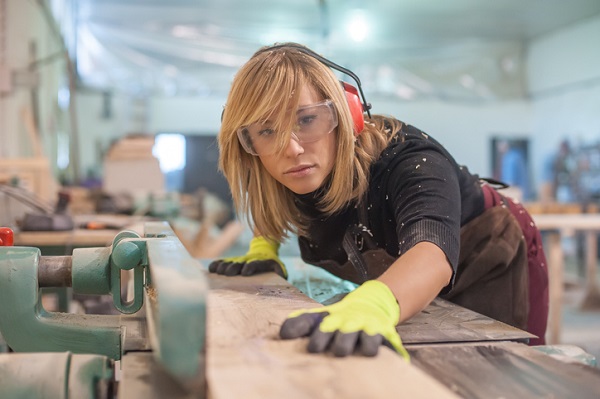
When you’re equipping yourself for the job, make sure you also pay special attention to:
- Clothing (avoid baggy, floating clothes that might get caught in the machinery)
- Jewelry (a long chain of loose bracelet might also be a hazard)
- Hair (if you’ve got long hair, make sure it’s tied up so it doesn’t get caught in the equipment)
3. Get to Know Your Tools and Equipment in Cabinet Making Training
Another important aspect of safe woodworking practice is the equipment that you are using. You’ll learn in cabinet making training about how to safely use woodworking tools and equipment. You should know what tool is required for what job, and you should know how that tool can be used most effectively. You should always verify that the tool is in adequate condition. For example, there is common a misconception that a sharp blade is more dangerous than a dull blade when, in fact, a dull blade risks getting caught or kicking.
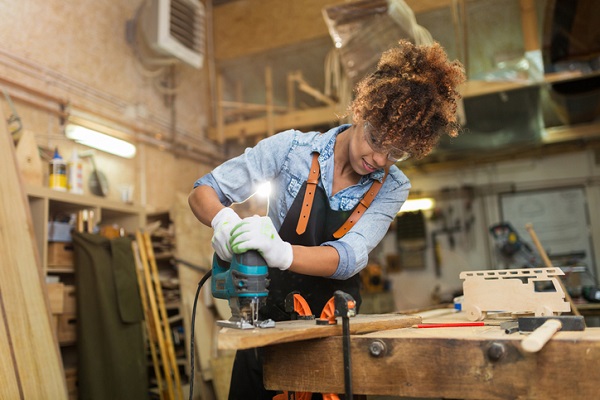
Soliciting help is another important part of safety. If you are operating a tool with which you have little experience, or if you know that a specific task will be easier with the assistance of a fellow woodworker, then it might be a good idea to get help. Be careful, however, to only get help from people who are properly trained!
Are you interested in cabinet making courses?
Check out North American Trade Schools to learn about our programs.