Category: Cabinetmaking
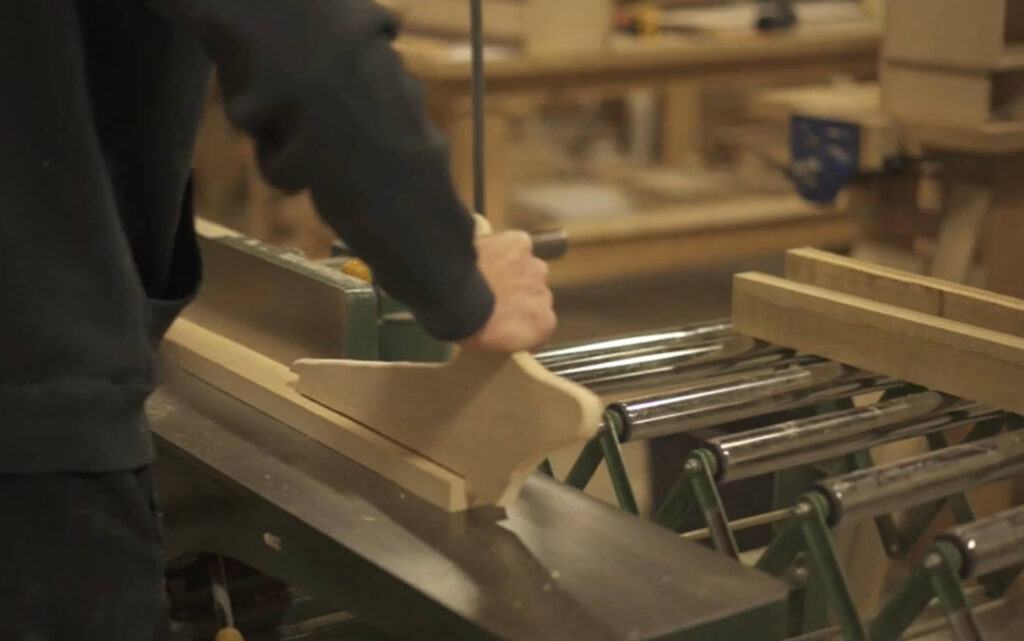
If you consider yourself a creative person, you may wonder how to channel this personal attribute into a fulfilling and lucrative career. Though plenty of planning and hard work lie ahead, it is possible to turn your dream into a reality, and we can help you!
Are you passionate about crafting beautiful, functional pieces of furniture? Do you dream of turning your love for woodworking into a profitable career? If so, cabinetmaking training at North American Trade Schools (NATS) could be your ticket to entrepreneurship. Keep reading to discover how we’ll equip you with the skills and competencies to thrive in your future entrepreneurial endeavors.
Why Cabinetmaking Makes a Profitable Business
Cabinetmaking is both an art and a science that combines creativity with precision. As a cabinetmaker, you can transform a simple piece of wood into a stunning piece of furniture that can last for generations. What sets cabinetmaking apart is the demand for custom, high-quality work.
In an era where mass-produced furniture is the norm, there’s a growing market for bespoke pieces that add a personal touch to homes and businesses. This demand presents the perfect opportunity for skilled craftsmen to establish a niche in the market. What sort of skills should you acquire to prepare for success in your future cabinetmaking business? Let’s explore!
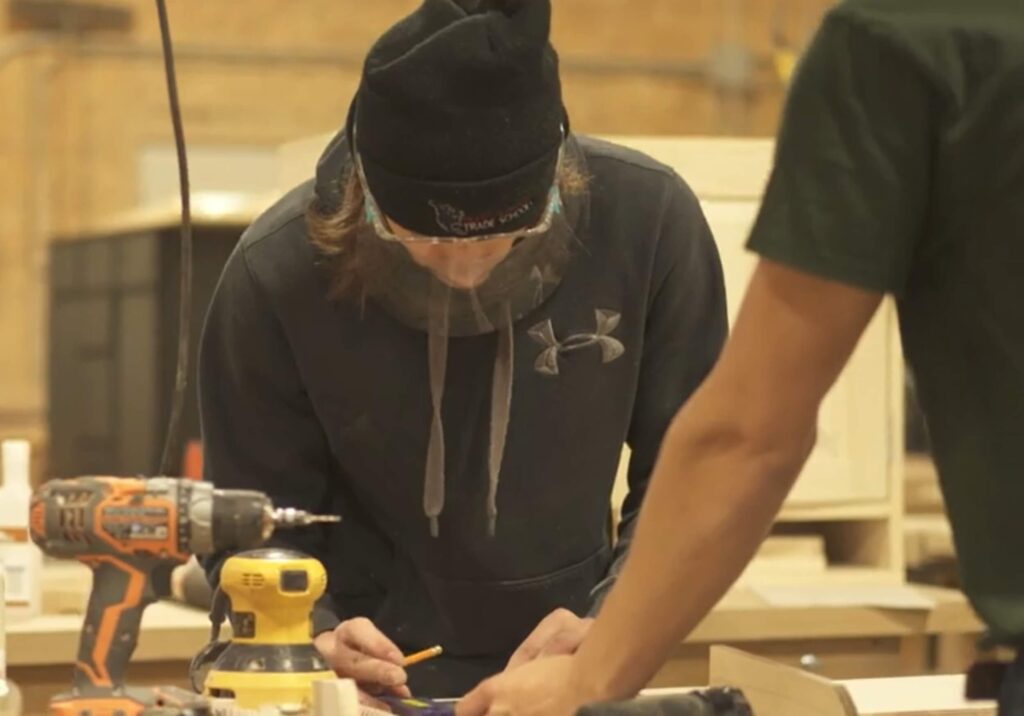
Skills You’ll Acquire in Our Cabinetmaking Training Program
At NATS, we understand that a successful cabinetmaker needs a strong foundation in technical skills and business acumen. That’s why our comprehensive cabinet making training covers everything from the basics of woodworking to advanced techniques in design and construction. Here’s a glimpse of what you’ll learn:
- Cabinetmaking Fundamentals: Master hand and power tools, understand the properties of different materials, and learn essential woodworking techniques.
- Cost Estimation: Learn how to execute your projects in an economically sound manner and how to price your services appropriately.
- Drawing and Blueprint Reading: Learn how the design of cabinets works and how to interpret and follow drawings accurately.
Turning Your New Skills Into a Career
After cabinetmaking college, you’ll possess unique skills that can be the foundation of a successful career. With woodworking, design, and construction expertise, you can offer custom-made furniture and cabinetry that stand out in a market saturated with mass-produced items.
To turn your skills into a career, start by identifying your niche: luxury bespoke kitchens, custom office furniture, or unique storage solutions. Developing a strong portfolio showcasing your craftsmanship and design capabilities is crucial for attracting clients.
Networking with interior designers, contractors, and architects can also open new opportunities. Social media and a professional website can help showcase your work and reach a wider audience. Additionally, understanding the business side, such as pricing strategies, marketing, and customer service, is essential for turning their craft into a profitable venture.
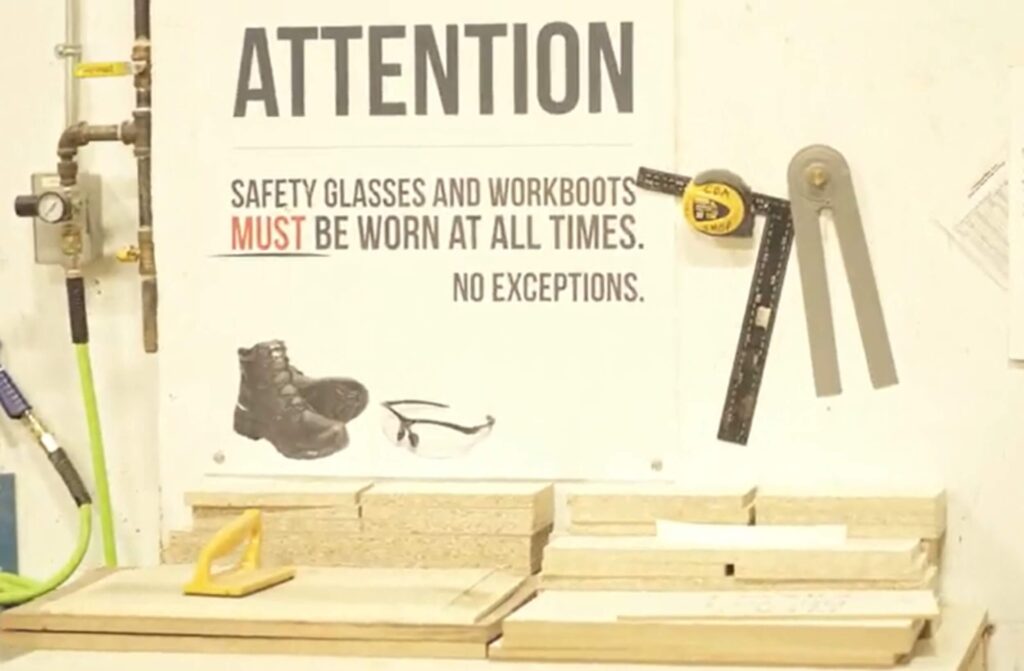
Combining your technical skills with entrepreneurial spirit allows you to create a career that fulfills its passion for woodworking and meets the growing demand for personalized, high-quality furniture and cabinetry.
If you’re ready to turn your passion for woodworking into a thriving career, NATS is here to help. Our cabinet making training can be a pathway to entrepreneurship for any student willing to use their strategizing and planning skills. With our experienced instructors, state-of-the-industry facilities, and a curriculum designed for success, you’ll be equipped to take on the world of cabinetmaking and make your mark as an entrepreneur.
Are you ready to earn your cabinetmaking diploma?
Contact North American Trade Schools for more information!
Is Cabinet Making the Right Career Path? A 2024 Guide For Cabinet Making Students
January 03, 2024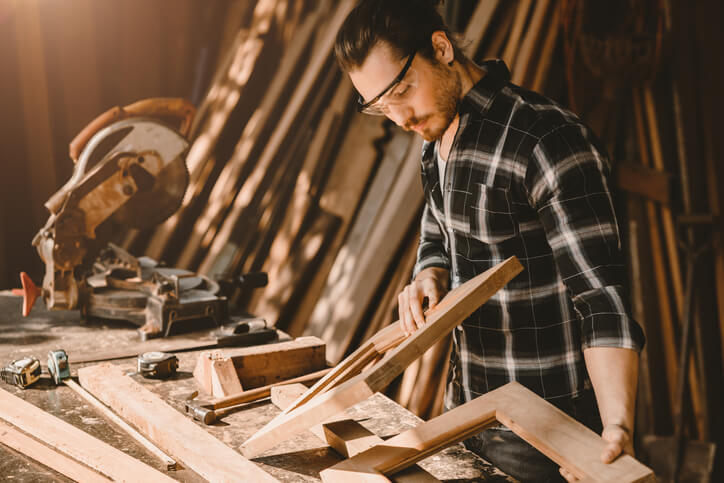
Are you a student contemplating a career in woodworking and craftsmanship? If so, cabinet-making might be the perfect path for you. In 2024, the demand for skilled cabinet makers will continue to rise, making it an attractive career option for those with a passion for woodworking and an eye for detail.
Ready to commit to a career in cabinet making in 2024? This field combines creativity with craftsmanship. With training options ranging from certificates to apprenticeships and a promising job outlook, it’s an ideal path for those passionate about building and design.
The Art and Craftsmanship of Cabinet Making
Cabinet-making is a centuries-old trade that blends artistry with practicality. As a cabinet maker, you will craft functional and aesthetically pleasing storage solutions, furniture, and fixtures. The beauty of this profession lies in its ability to transform raw materials into pieces of art that serve both practical and decorative purposes.
The modern cabinet maker is expected to possess a diverse skill set. From interpreting design blueprints to selecting and preparing materials, your expertise will be crucial at every stage of the cabinet-making process. Proficiency in woodworking tools, understanding various wood types, and mastering finishing techniques are just a few of the skills you’ll need to succeed.
In 2024, the demand for custom-made furniture and unique cabinetry will continue to rise. Homeowners and businesses seek personalized solutions that stand out in design and functionality. This shift in consumer preferences presents an exciting opportunity for cabinet makers to showcase their creativity and craftsmanship.
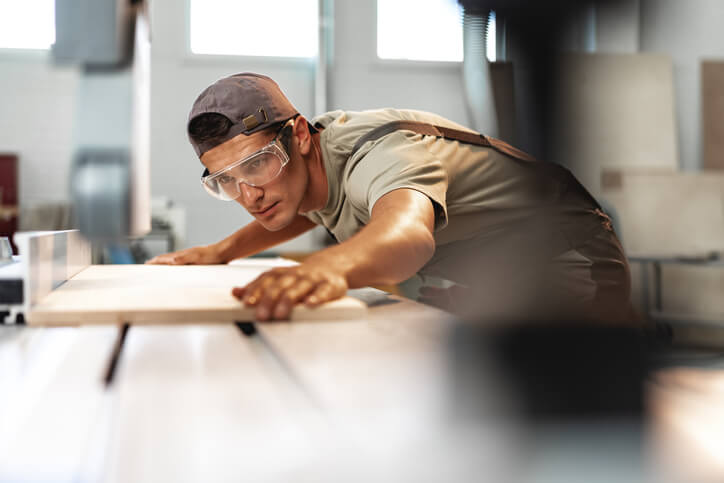
Education and Training Will Contribute To Your Cabinet Making Diploma
Pursuing a cabinet-making career, beginning with some form of formal education, can be highly advantageous. Many vocational schools and technical institutes offer comprehensive cabinet making training programs (such as NATS’ Cabinetmaking Diploma Program) that cover the fundamentals of woodworking, cabinet design, and construction techniques. These programs are also tailored to impart a broad range of skills essential in the field. This education equips students with practical, trade-level skills and instills a deep understanding of different materials and techniques used in cabinet making. These programs prepare students to enter the trade with confidence and proficiency, ready to take on the various challenges this creative and technical field presents.
Additionally, apprenticeships offer valuable hands-on experience. Working under seasoned cabinet makers, apprentices learn the trade’s practical aspects, from material selection to intricate joinery techniques. Remember, keeping up with the latest design trends and technologies is key to staying competitive in the cabinet-making industry.
Job Outlook and Career Advancement After Cabinet Making Training
With the growing interest in bespoke furniture and high-quality craftsmanship, the job outlook for cabinet makers is promising. The versatility of this skill set opens doors to various career paths, including custom furniture design, architectural millwork, and even entrepreneurship.
Experienced cabinet makers often find opportunities to advance into supervisory or managerial roles, overseeing production teams and projects. Some may start their woodworking businesses, catering to a niche market or collaborating with interior designers and architects.
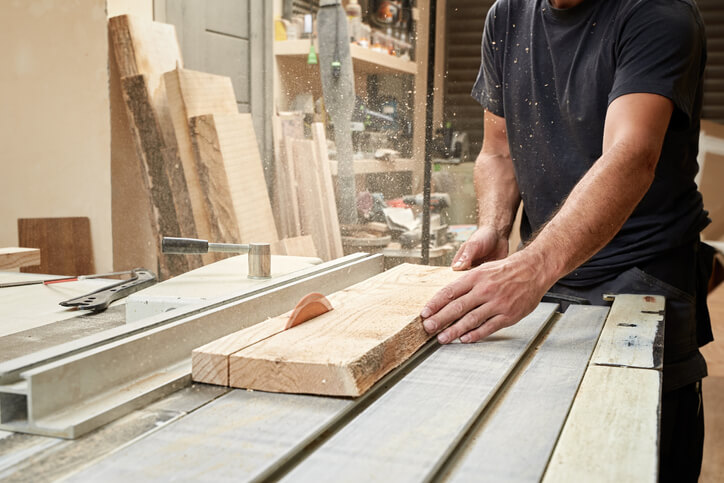
Is Cabinet Making a Good Career
So, is cabinet making a good career? Like any profession, cabinet-making comes with its challenges. The job’s physical demands, the precision required in measurements, and the necessity for patience are aspects that aspiring cabinet makers should be prepared for.
However, the rewards are significant – the satisfaction of creating functional works of art, the joy of seeing your designs come to life, and the potential for a lucrative career in a growing industry. On a more practical level, the financial rewards can be substantial, especially for those who establish a niche or start their own business. While the initial earnings might be modest, skilled cabinet makers are often in high demand, leading to higher earning potential.
Are you interested in obtaining your cabinet making diploma?
Contact NATS for more information.
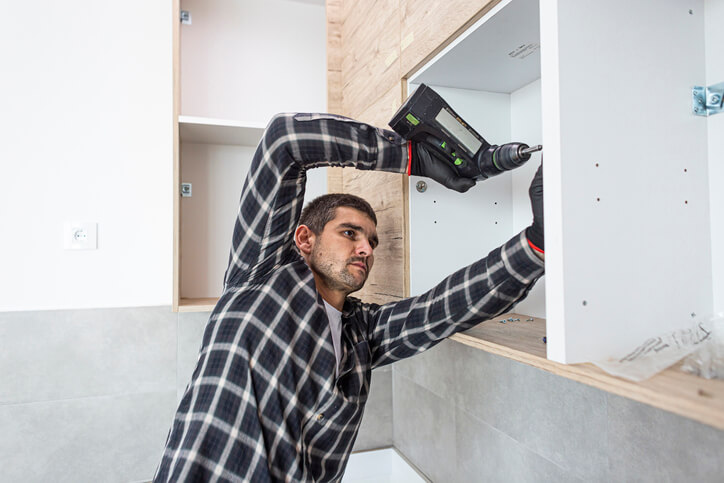
Cabinet making is a skill and an art. Whether you’ve just finished a professional course or are embarking on a DIY journey, crafting a cabinet with precision and care can be immensely satisfying. However, even after creating a beautiful piece, installation’s another critical step. And this is where many enthusiastic cabinet makers stumble.
Here are some common installation mistakes made that could be avoided by those who completed the cabinet making courses.
Failing to Check Measurements and Levelness
One of the golden rules in woodworking and cabinet installation is “Measure twice, cut once.” It’s easy to get excited and rush through measurements, but even a few millimeters off can spell disaster for your installation. Incorrect measurements can lead to gaps, misalignment, and a cabinet that doesn’t fit or function as intended. As it is one of the fundamentals discussed in the cabinet making training, always double or triple-check your measurements before making any cuts or installations.
A flawlessly crafted cabinet can be ruined by uneven installation. Cabinets that are not level can lead to uneven doors, difficulty opening or closing, or even long-term structural issues. Always use a trusted level system during installation and make necessary adjustments to ensure your cabinets sit perfectly as required.
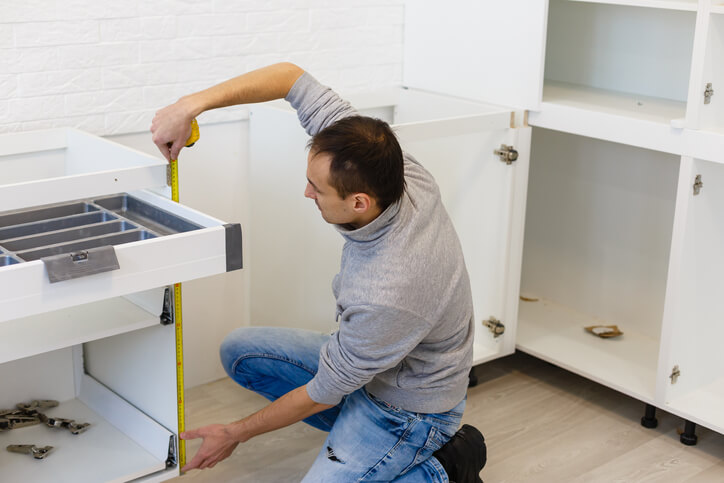
Overlooking Wall Studs and Ignoring Spaces or Fillers
Mounting cabinets directly on drywall without anchoring them to studs is a recipe for disaster. Over time, the weight can cause the cabinets to pull away from the wall, leading to damage and potential injury. Always locate and mark the wall studs and ensure that your cabinet screws penetrate these studs for a secure installation.
Beyond this, every room has quirks, and the walls must not be straight. Spacers or fillers are essential to address these irregularities. They help ensure that your cabinet fits perfectly and has a professional finish. Ignoring them can lead to unsightly gaps or cabinets that jet out in odd ways.
Forgetting the Toe Kick as Taught in the Cabinet Making Courses
The toe kick is that recessed space at the bottom of floor cabinets, and it’s not just for aesthetics, as most cabinet making courses emphasize. It provides a comfortable space for your feet as you stand at the counter. It might seem like a minor detail, but omitting a toe kick can make your kitchen or workspace uncomfortable and can detract from the overall finished look.
Using Inadequate Hardware and Neglecting the Finish
It’s not just about the wood. Screws, brackets, and other hardware are crucial in securing your cabinet. Skimping on or using the wrong hardware can lead to wobbly cabinets or, worse, cabinets that fall apart after a short period. Invest in high-quality hardware that’s designed explicitly for cabinetry.
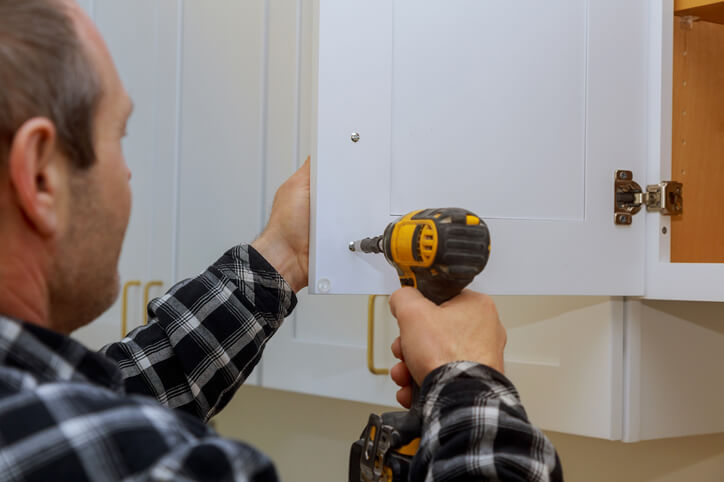
Also, after installing your cabinet, finishing it with sealants or paints that protect the wood and enhance its appearance is essential. This step will make your cabinet look polished and professional and protect against moisture, stains, and everyday wear and tear.
Are you interested in a cabinet making diploma?
Contact NATS for more information.
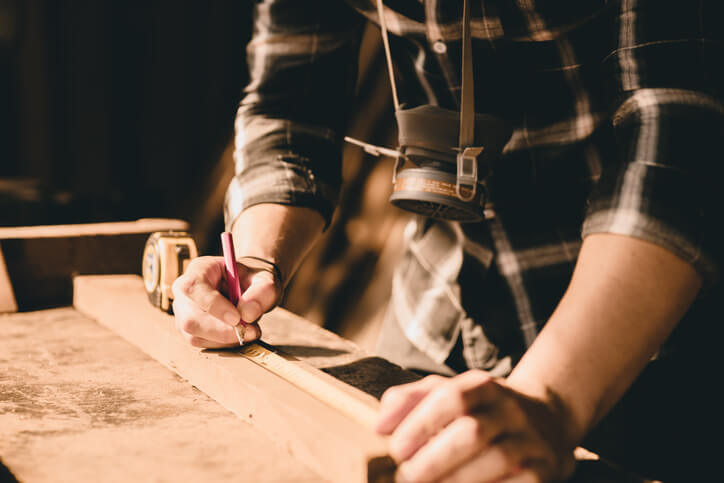
Have you ever wondered what life looks like for a cabinetmaker after completing cabinet-making courses? Cabinet makers craft and set up cabinets, desks, and other premium furnishings crafted from wood, plastic laminate, and solid surface compositions. They employ woodworking machines and power tools to cut, mold, and structure these items precisely.
Cabinetmaking is a unique and skilled craft that requires precision, creativity, and dedication. In this blog post, we’ll take you through a typical day in the life of a cabinetmaker who has honed their skills through cabinet-making courses, showcasing the challenges, joys, and rewards of this profession.
Blueprint Analysis and Dimension Verification
A cabinetmaker starts the day by meticulously inspecting the blueprints of the day’s project. Whether it’s a custom cabinet for a client’s kitchen or an exquisite piece of office equipment, understanding the design down to the smallest detail is crucial. One of the first tasks involves verifying dimensions. With a keen eye, they ensure every measurement on paper matches the intended physical output. This step ensures that the final piece adheres strictly to specifications, ensuring durability, aesthetics, and functionality.
Post blueprint analysis, the cabinetmaker shifts focus to raw materials. Selecting the right lumber stock or an appropriate wood substitute is a delicate choice, influenced by design requirements and client preferences. With a blueprint, they measure and mark the dimensions of the chosen material. Every mark has to be exact; after all, ensuring a tight fit and a top-quality product lies in these initial markings.
Machine Operation and Component Assembly
As the workshop hums with activity, the cabinetmaker gets into the heart of the process. Their cabinet-making training has made them adept at handling various woodworking machines – power saws, jointers, morticers, tenoners, molders, and shapers. Each machine has a specific role, from cutting and molding to shaping the wood or its substitute. Operating them requires skill, and after their courses, the cabinetmaker wields these machines with confidence and precision.
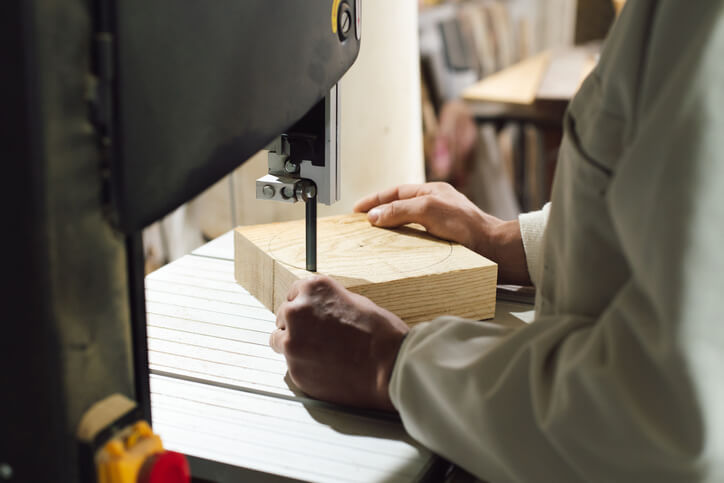
As individual components get fashioned, they are gradually assembled throughout the day. This assembly isn’t merely about joining pieces; it’s an art. The alignment must be perfect, and every component, whether a door hinge or a cabinet shelf, needs to fit seamlessly.
Finishing and Quality Inspection After Cabinet-Making Training
After assembly, it’s time to refine the cabinet’s surface. This involves sanding down any rough edges and applying a finish to enhance the wood’s natural beauty and protect it from wear and tear. Cabinet Makers often have a selection of stains, paints, and varnishes, allowing them to achieve the desired look for each project. This step can be time-consuming, but it’s essential for achieving a polished and professional appearance.
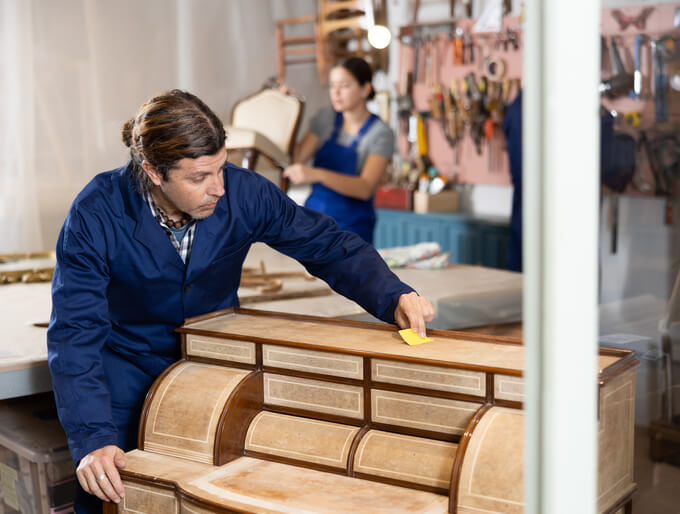
Before any project leaves the workshop, it undergoes a thorough quality control inspection. As they have learned from their cabinet-making courses, cabinetmakers meticulously check for imperfections, ensuring that the piece meets their high standards of craftsmanship. They also verify that all components, such as drawers and cabinet doors, function correctly. This attention to detail ensures that the final product will delight the client.
Once the cabinetmaker is satisfied with their work, it’s time to invite the client for a final inspection. This is a rewarding moment, as it allows the cabinetmaker to see the joy and satisfaction on the client’s face as they take possession of their custom-made piece. After client approval, the cabinet is carefully packed and delivered to its new home.
Are you interested in a cabinet-making diploma?
Contact NATS for more information.
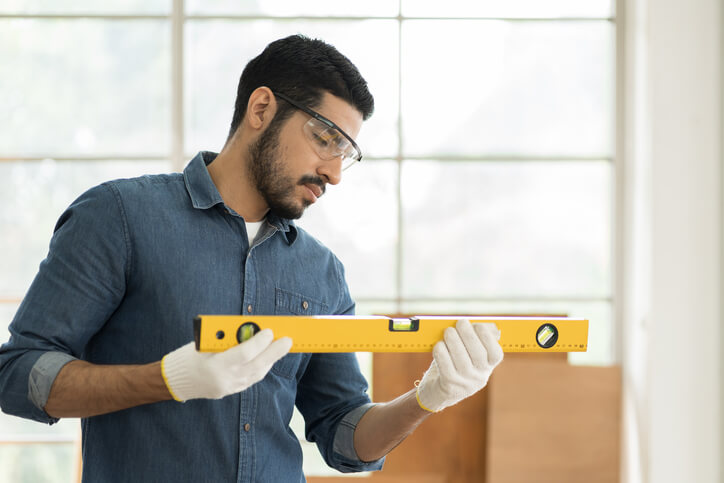
This obviously does not apply to everyone, but there’s something so wholesome and fulfilling about rescuing items (or constructions) from potential ruin and restoring them to their original glory. If this desire to repair and add value applies to you, you probably are already considering home renovation college.
One area that often requires attention during a renovation is wood restoration. Wood can add warmth and charm to any home, but over time, it may lose its lustre and become damaged. Wood restoration is also one of the most common projects faced by home renovation professionals, so here are four wood restoration tips to help you bring new life to wooden elements in any home.
1. Assess the Condition of the Wooden Element
Before embarking on the restoration of your piece, it’s essential to conduct some research to ascertain its value. Carefully examine the furniture for any marks or labels that might provide insights into its origin or manufacturer. If you suspect that it holds significant monetary or historical worth, it’s advisable to consult with a professional before proceeding with any restoration work. It’s also a good idea to take detailed photographs of any markings or tags as documentation. Refrain from stripping or sanding a collectible antique’s finish until you have a clear understanding of its value, as doing so could potentially diminish or even eliminate its worth.
As you’ll discover in home renovation training, it’s crucial to assess the condition of the wood you’re working with. Take a close look at the surfaces, checking for signs of rot, pests, or water damage. Look for cracks, warping, or discolouration. Understanding the extent of the damage will help you determine the best approach to restoration. Minor issues might only require sanding and refinishing, while more severe damage could require repair or replacement.
2. Prepare the Surface Correctly as Taught in Home Restoration College
Proper surface preparation is vital for achieving a successful wood restoration. To give your furniture a comprehensive cleaning, start by using a sponge and a solution of warm water and vegetable-based oil soap. Scrub the surfaces of the furniture thoroughly to remove any dirt and grime. Rinse the surface with clean water and allow it to dry completely before moving on to the next step.
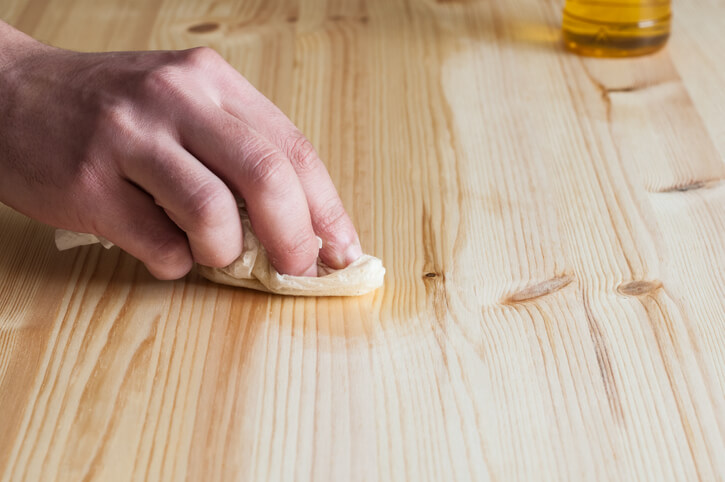
For intricate or detailed pieces, employ a soft toothbrush to access hard-to-reach areas and clean the nooks and crannies effectively. In case there are tight spots that are difficult to reach, you can fashion a slender wooden dowel rod into a pointed tip, similar to sharpening a pencil. This sharpened end can then be utilized to carefully extract grime from those narrow spaces.
If you have stubborn stains or old finishes, you may have to scrape them off with sandpaper or a wood stripper.
3. Choose the Right Finishing Method
The choice of finishing method will depend on the desired look and the type of wood you’re working with. Some popular options for wood restoration include staining, painting, and applying varnish or oil-based finishes. Staining can enhance the natural beauty of the wood, highlighting its grain and texture. Painting can provide a fresh and uniform appearance, while varnishes or oils offer protection and durability. Research different finishing techniques and consult with professionals to determine the best option for your specific project.
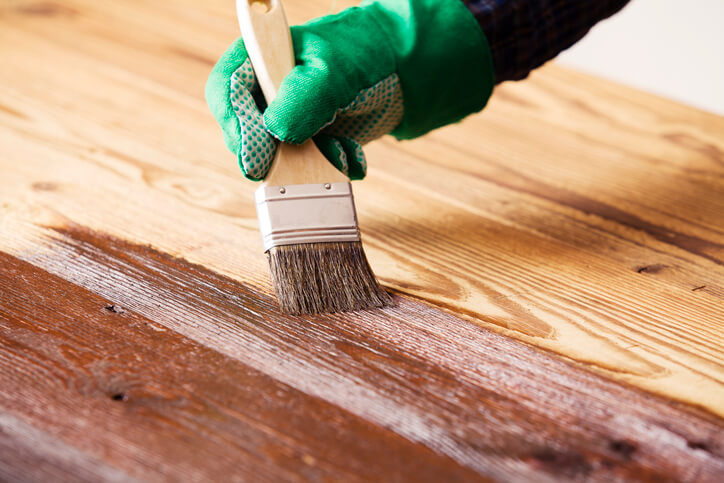
4. Home Renovation College Educates on Proper Restoration Techniques
Wood restoration requires careful attention to detail and proper technique, just as our home renovation courses explain. When sanding the wood, start with coarse-grit sandpaper to remove any imperfections, then gradually switch to finer grits to achieve a smoother surface. Always sand in the direction of the wood grain to avoid scratches. If repairs are necessary, use suitable wood fillers or epoxy to fill cracks and holes, ensuring a seamless finish. Apply finishes evenly, following the manufacturer’s instructions, and allow sufficient drying time between coats.
Are you looking for a world-class home renovation college?
Contact NATS for more information.
4 Essential Woodworking Techniques for Those in Cabinet Making Training
August 11, 2023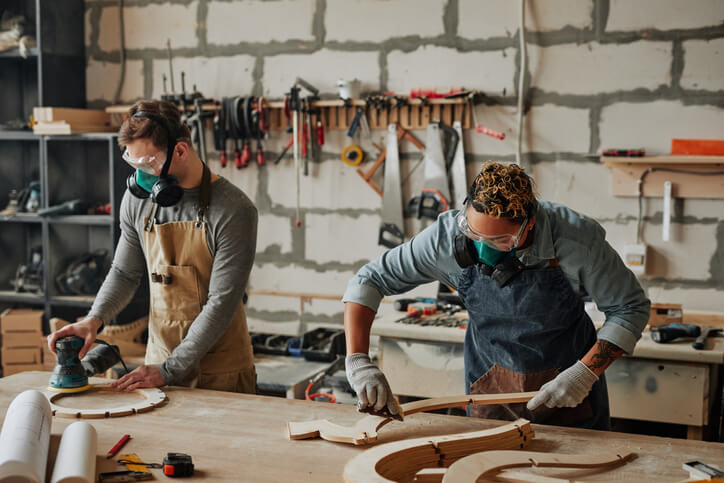
Like many other handcrafts, cabinet-making requires the use of several intricate skills and techniques. The accuracy, precision, and skill that go into it can only be obtained from quality learning and constant practice. This is why we have dedicated and passionate instructors at the North American Trade Schools (NATS) to pass down their wealth of experience to willing learners. If you choose a cabinet making career, you’ll be interested in the woodworking techniques discussed in this article.
Milling After Cabinet Making Training
Milling involves the conversion of rough lumber into symmetrical and precise work pieces, and it’s one of the most useful techniques you’ll learn during cabinet making training. It is the wood preparation process that begins with flattening one face of the board at the jointer and then smoothening the board’s opposite face at the planer. Next, you can make the board’s remaining edge true to the other by using a table saw and a chop saw.
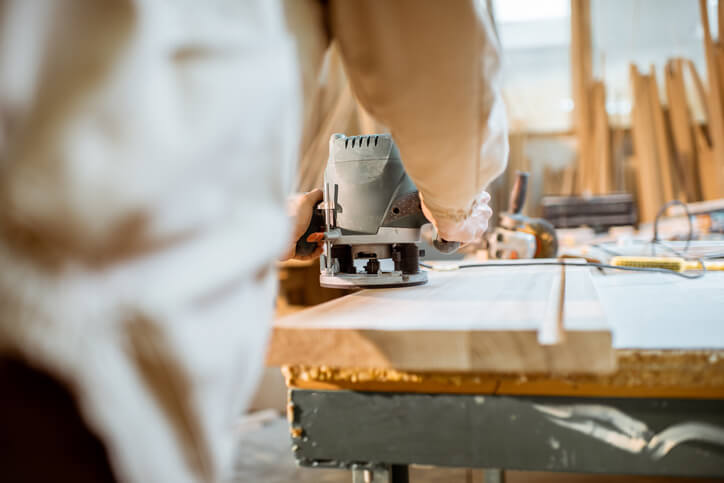
Jointing
Jointing is the process when you smooth one face of the workpiece so you can reference it from that face whileTruing up the workpiece. During your journey through the cabinet making certificate program you will be shown the importance of good jointing techniques.
Planing
Planing is a surface-smoothing technique that rids the wood surface of any defects and excess material. You must learn to use a hand or electric planer to carry it out. When properly done, the lumber board will turn out with an even thickness across its required length. This is after you must have used the jointer to flatten one face of the board.
Sawing
Sawing is unarguably one of the most important parts of cabinet making. Our cabinet making courses provide insights into how to use several sawing tools and the various techniques for handling them. These tools include the chop saw, handsaw, table saw, circular saw, and chainsaw, among other sawing tools used for different purposes and project types. The key to using some of these tools is maintaining the right posture to achieve maximum impact without endangering yourself.
Drilling and Boring
While drilling creates holes in the wood, boring further enlarges the hole by removing excess material along the depth of the opening. Both processes will need precise control of the work tools to create openings with the right fit, and this requires adequate knowledge of the use of the proper drilling and boring tools and their accessories.
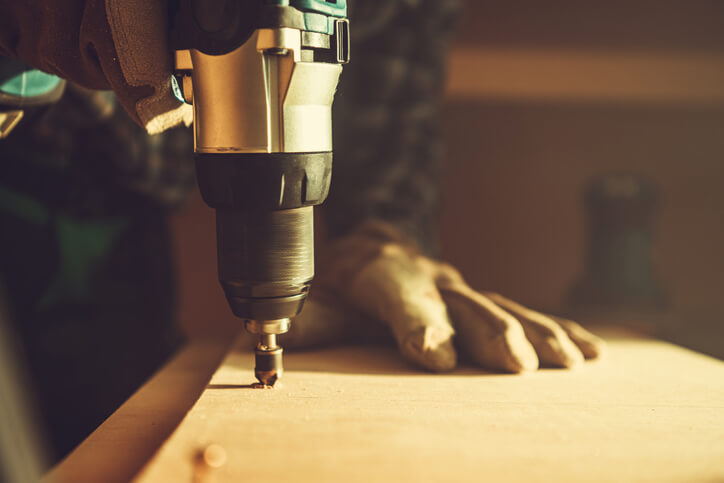
While using the drilling press, ensure the drill is at the correct speed, as drilling too fast can break the drill bit and create poorly machined holes. And while drilling in deep cuts, take out the drill at intervals to cool and clean the bit.
Finishing
This is the last stage of the cabinet-making process. It involves a series of actions, including sanding, filing, and rendering, all of which are taken to add finishing touches to the cabinet. For the best results, start with coarse grit sandpaper and sand in the board’s grain direction to create a fine grit surface free of scratches.
Top it off by applying thin coats of the selected finish across the entirety of the cabinet while looking out for joints and other hidden parts. Lightly sand on the cabinet surface before applying the topcoat, if necessary.
Want to earn your cabinet making diploma?
Contact NATS to learn how you can get started.
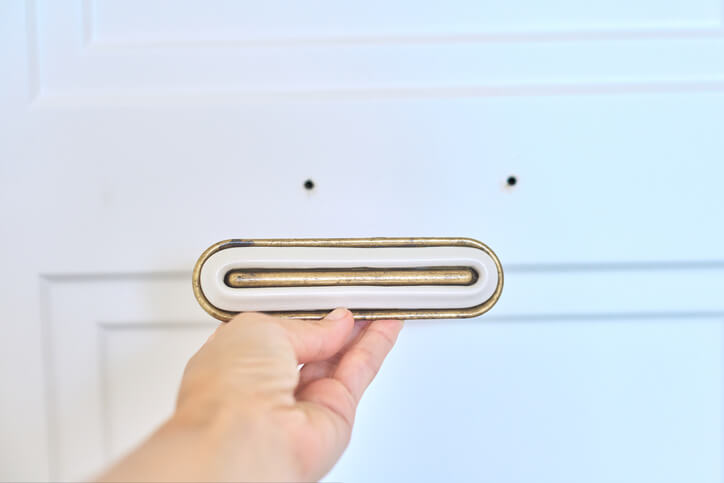
Cabinet making is fun and rewarding career path that allows you to use plenty of creative licenses. Many exciting decisions exist in this area, from the wood you choose to work with to the style your project emulates.
During cabinet making training, you’ll learn about the different types of hardware you can use to add the finishing touches to your cabinets. Handles on cabinet doors are essential, as they contribute to everyday ease of use and present the perfect opportunity to make a significant style statement. Read on to learn what you should consider when choosing hardware for your cabinets once you begin your career.
Know Different Hardware Styles After Cabinet Making Training
During cabinet making training and throughout your career, you’ll see and learn about a vast array of cabinet door handle styles. Knowing the characteristics of each style and what design components complement one another will help you make the right decision for your clients. Most cabinet hardware falls under one of the following style categories:
- Contemporary: Sleek lines, a neutral colour palette, and simplicity are hallmarks of the contemporary style. If you’ve built cabinets for clients wanting a contemporary space, opt for something simple and streamlined. For example, linear bar handles are a trendy contemporary option to create a harmonious effect that your clients are sure to love.
- Traditional: There’s a reason why the traditional style has stood the test of time. The ornate details and curved shapes create a look best described as ‘fancy.’ This hardware style looks best in a space with plenty of opulent details and pays homage to antique decor. Traditional-styled cabinet door handles can be added to a modern space for an eclectic touch.
- Rustic: The ‘farmhouse’ or rustic style has recently gained popularity among clients, particularly in kitchens. Rustic finishes tend to produce a homey look where simplicity is favoured with industrial details. Rustic hardware is simple but balanced, typically combining straight and curved lines.
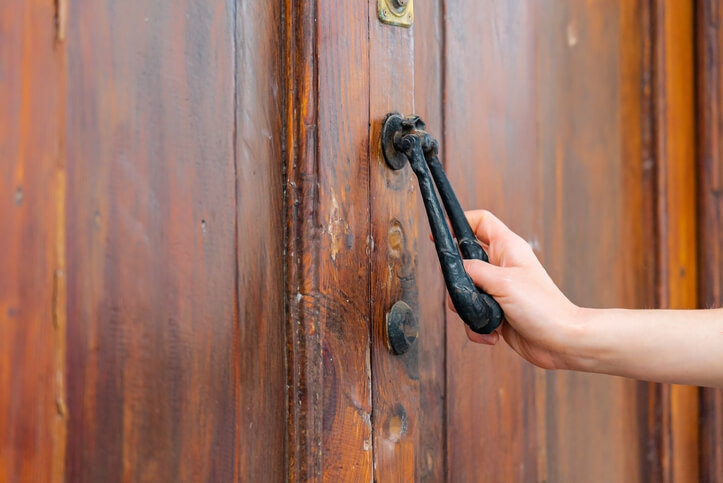
Remind Clients to Keep Comfort in Mind When it Comes to Cabinet Hardware
Cabinet doors can be closed and opened multiple times throughout the day, depending on their location. After Cabinet Making training, it’s important to remind clients to consider comfort in order to maximize the overall results of the project.
Providing clients with samples of each style are so they may test each handle’s feel and functionality will help them make the right decision. Ask them to pay close attention to how each handle feels in their hands, whether there are any imperfections in the material, and how easy (or difficult) it is to open a door with the handle. Comfort plays a significant role in the overall user experience of cobinet making jobs.
Help Clients Choose the Right Finish After Cabinet Making Training
The finish will likely be the most noticeable characteristic of the hardware your client chooses for their cabinets. While chrome and brushed nickel are some of the more common choices, there are many other options your clients can choose from.
Regarding kitchens and bathrooms, there’s a common belief that the hardware should match the faucet; however, this isn’t necessary. Simply make sure that clients know that the finishes of their hardware should compliment (not necessarily match) other finishes in the space.
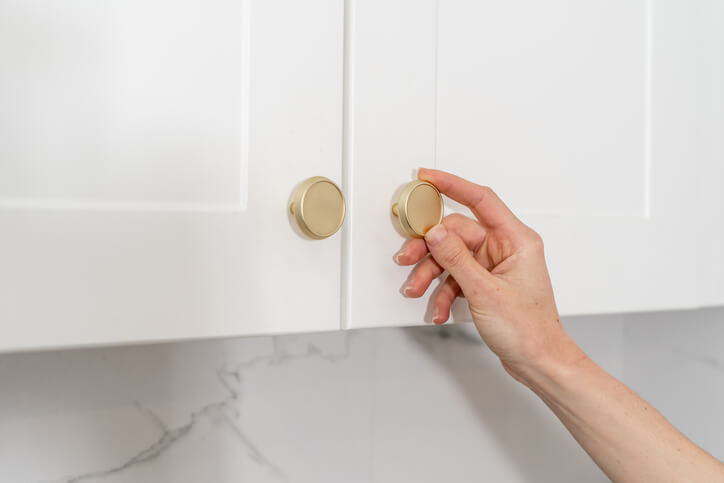
Our Cabinet Making diploma program teaches students about the wood selection process, as well as how to read drawings, operate woodworking machines, and practice the arts of cabinet making. Hands-on training is a hallmark of our program, and our students are fully prepared to work on various cabinet making and installation projects with confidence and mastery.
Are you ready to start Cabinet Making courses?
Contact NATS to learn how you can get started.
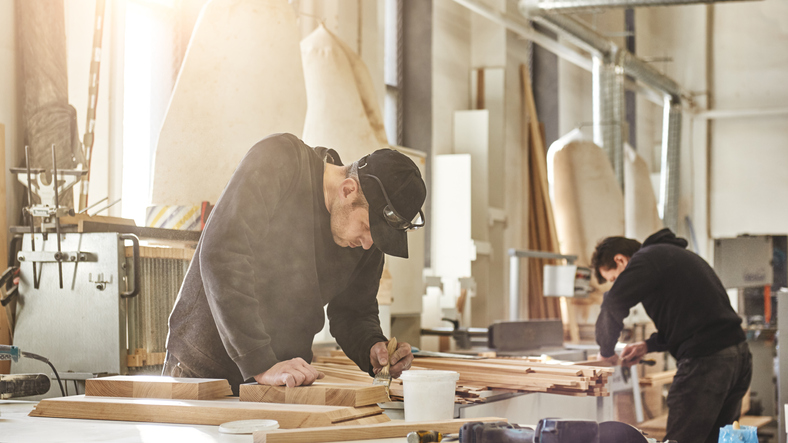
Cabinet making is an intricate and complex woodworking skill that requires precision, accuracy, and attention to detail. As a cabinet making school student, you’ve probably spent much time and effort crafting your cabinets to perfection. But what about finishing them? While cabinet making requires a high degree of technical skill, it’s the finishing that gives a cabinet its final touch of class and sophistication
The final step in the process can make or break the overall look and feel of your creation. Here are five finishing tips to help you achieve a professional-looking finish for your cabinets.
1. Prepare Your Surfaces After Cabinet Making Training
Before you start applying any finish, make sure your surfaces are properly prepared. This means sanding them down to remove any rough spots or imperfections. Start with a coarse grit sandpaper and work your way up to a finer grit, just as you were taught in cabinet making training. Make sure to sand in the direction of the grain to avoid creating any scratches.
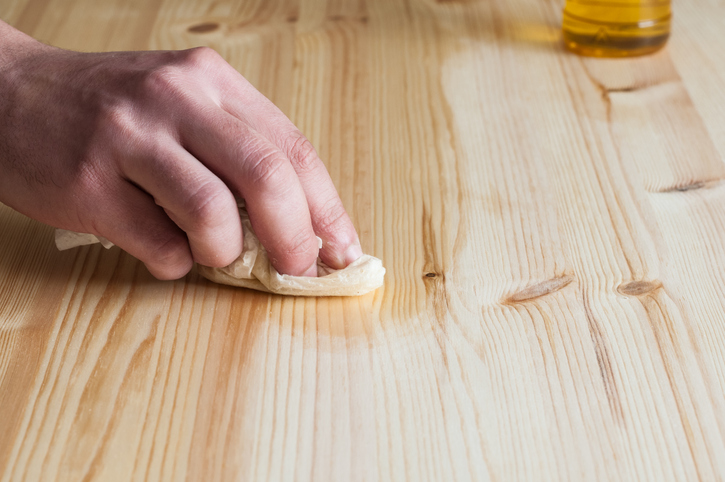
After sanding, wipe down the surfaces with a tack cloth to remove any dust or debris. Pay attention to the insides of your cabinet and cover exposed hardware with tape.
2. Choose the Right Finish
There are many different types of finishes to choose from, each with its own benefits and drawbacks. The type of finish you choose will determine the final look and feel of your cabinets, as well as how they will stand up to wear and tear over time. Some popular options include lacquer, varnish, and oil-based finishes. Consider the type of wood you’re working with, as well as the desired look and feel of the finished product. If you’re unsure which finish to use, talk to your instructor or a professional in the field.
3. Apply Thin Coats
When applying your chosen finish, it’s important to remember that less is more. If you apply too much finish at once, it may drip and have uneven coverage, which can be difficult to fix later.
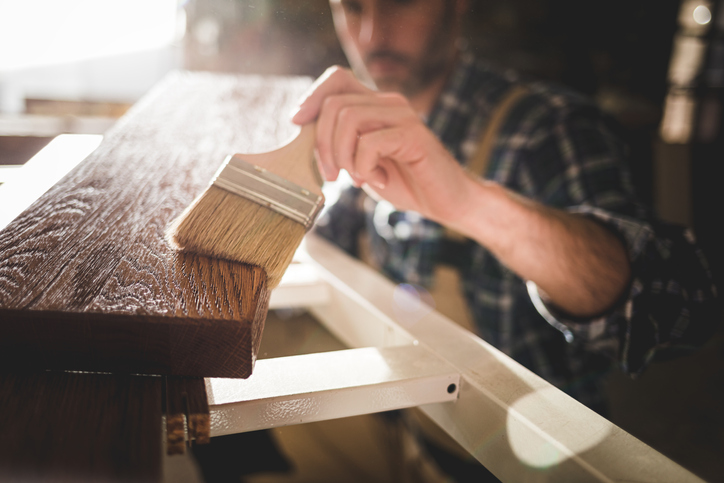
To achieve a thin coat, apply a small amount of finish to your brush or spray gun. Then, work the finish into the wood, covering the entire surface evenly. Be careful not to overwork the finish, as this can result in drips and an uneven appearance. Use a brush or spray gun to apply the finish, making sure to follow the manufacturer’s instructions for application and drying times.
4. Sand Between Coats
After each coat has dried, use fine-grit sandpaper to lightly sand the surfaces, drawing inspiration from insights gained in your cabinet making courses. This will help remove any imperfections and ensure that the next coat adheres properly. Be careful not to sand too much, or you may remove some of the finish.
5. Finish With a Topcoat
Once you’ve applied your final coat of finish, consider adding a topcoat to protect the surfaces from wear and tear. A topcoat can also help enhance the appearance of the finish, making it look more vibrant and lustrous. Some popular topcoat options include polyurethane and wax.
Remember to prepare your surfaces properly, choose the right finish, apply thin coats, sand between coats, and finish with a topcoat. With these tips in mind, you’ll be able to create beautiful, high-quality cabinets that will stand the test of time.
Are you ready to begin your training at cabinet making school?
Contact NATS to learn how you can get started.
Blueprint Reading: 4 Best Practices to Keep in Mind After Cabinetmaking Training
January 10, 2023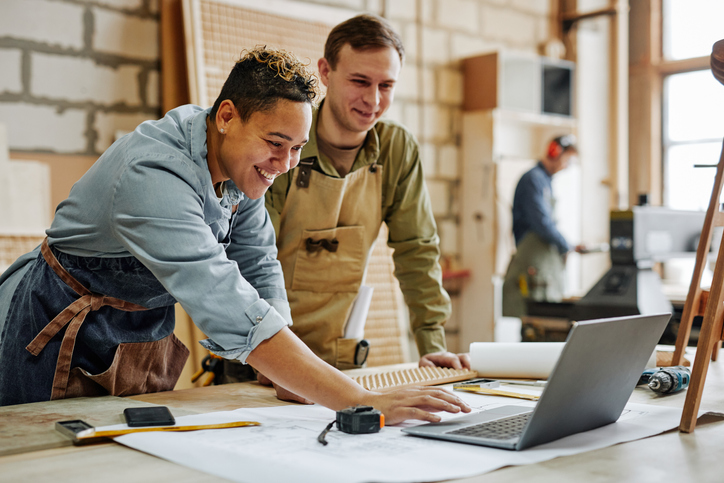
Cabinetmaking and other construction projects require detailed plans to ensure that all key elements are in the right place, that the project is compliant with safety codes, and that it meets customer expectations. That’s where blueprints come in. They are two-dimensional technical drawings that illustrate the design of a project in detail. By looking at a blueprint, you should have a good idea of a project’s dimensions, materials, and the exact placement of each component.
Without any experience in cabinet making or construction, blueprints may seem complex at first glance; however, with the right training, you can hone this essential skill and approach each project confidently. Read on for blueprint best practices you can keep in your arsenal throughout your training and career.
1. Always Begin With the Title Block
The title block will stand out to you when you look at a blueprint after Cabinetmaking training. It contains basic introductory information that will come in handy throughout your project. That’s why it’s an excellent idea to look at the title block before you begin a project. In addition to the project name and number, this part of the blueprint contains contact information for the designer in case you spot an error or anything that needs further clarification. You’ll also see an index which is a reference list of all the drawings in the set of plans.
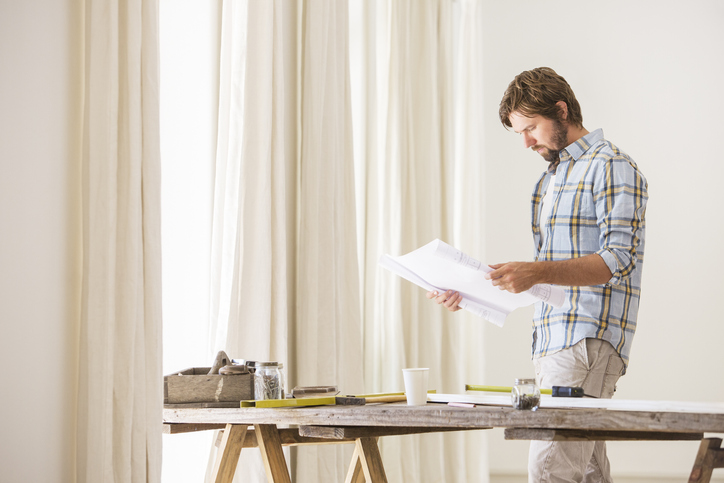
2. Study the Legend to Understand Your Project Fully
Similar to what you would see on a map, the legend on a blueprint decodes the symbols found throughout a design to represent key components of the project. While there are universal symbols, there are also industry-specific symbols, and some companies even have their own custom symbols. Studying the legend right away will make it much easier to understand your blueprint since you’ll know exactly what each symbol represents. The legend may also contain the standard scale to give you a good idea of the project size.
3. Pay Close Attention to the Notes
When interpreting a blueprint after Cabinetmaking school, you’ll find that notes are often littered throughout a set of plans. For this reason, it’s wise to set time aside for a thorough reading of the entire project plan to ensure that you don’t miss any important specifications. As they study the notes in a blueprint, many experts make notes of their own with any questions and concerns about the design. It’s best to clarify any unknowns before getting started to ensure that no materials, power, or time are wasted.
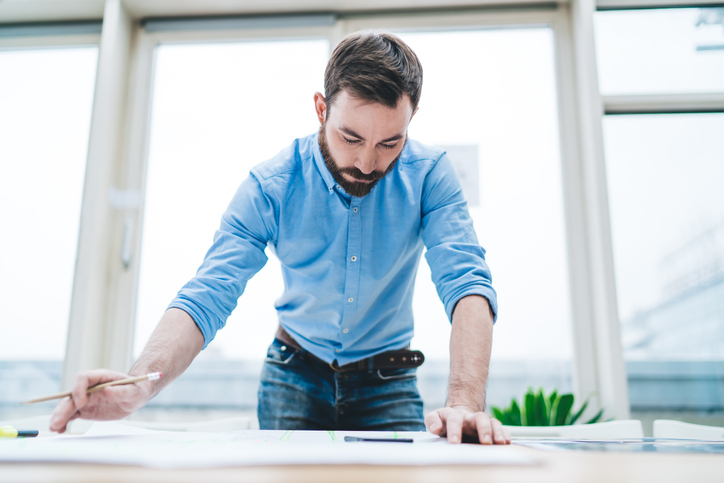
4. Develop a Trained Eye in Cabinetmaking School
As with most construction skills you’ll develop in training, and throughout your career, mastering blueprint interpretation will require a lot of practice. For this reason, you’ll want to choose a Cabinetmaking training program that provides ample opportunity to read and execute plans effectively. With time, you’ll develop a trained eye and reading blueprints will become second nature. With this skill set, which you’ll develop in our Cabinetmaking Diploma Program, you can go on to enjoy an exciting career in cabinetmaking and installation, store fixture making, architectural millwork, and more.
Ready to earn your Cabinetmaking Diploma?
Contact NATS for more information!
Cabinet Design Techniques that Those in Cabinetmaking Careers Will Want to Remember
December 08, 2022If you’re considering a career as a cabinetmaking professional, you’ll be an expert in the art of designing, building and installing different styles of cabinets. Not only will you be selecting the wood you’ll work with, but you’ll also operate different woodworking machines. You will also be responsible for putting together blueprints, using different techniques for assembling and finishing cabinets, and more. By mastering different design techniques during your cabinetmaking training, you’ll be able to perform a wide range of cabinetry projects–enabling you to accommodate your customer’s needs.
There are many different types of cabinets that can be installed in kitchens, bathrooms, and other rooms in a building. The more design techniques you are familiar with, the more advanced your skill set will be. Below, explore several cabinet styles and design techniques that you’ll perfect after cabinet making courses.
[Infographic] Cabinet Design Techniques that Those in Cabinetmaking Careers Will Want to Remember
Contemporary Cabinets
What are contemporary cabinets?
- Minimalist & streamlined appearance
- Little decoration, flat surface
Materials used:
- Wood/plywood or manmade materials
- No raised panels
- Box/case construction to create a simple design
Modern Cabinets
What are modern cabinets?
- Angular/curved in appearance
- Mixed materials create a distinct look
How they’re built:
- Finished with plastic laminate or wood veneer
- Horizontal grain pattern
- Mixed materials used include wood, frosted glass, metal
Tuscan Cabinets
What are Tuscan cabinets?
- Made from high-quality wood (cherry, maple)
- Deep colours create an elaborate appearance
How they’re built:
- Cabinet doors accented with raised panels
- Paired with metals such as bronze, copper, and brass
Country Cabinets
What are country cabinets?
- Built from woods like pine, maple, hickory, cherry, and oak
- Durable and long-lasting
How they’re built:
- Often feature raised-panel doors and beadboard
- Painted and glazed to create a colourful appearance
With these techniques and styles under your belt, you’ll be able to create a set of custom cabinets that will please any customer!
Sources:
https://www.hgtv.com/design/remodel/kitchen-remodel/kitchen-cabinet-styles
https://extremehowto.com/cabinet-building-basics-for-diyers/
https://cabinetsbydesignaz.com/kitchen-cabinet-construction-methods/
https://www.masterbrand.com/get-started/design-your-room/cabinet-101